The membrane reactor is a highly efficient water treatment technology that combines membrane separation technology with traditional biological treatment processes to achieve water purification and pollutant removal. The following is a detailed introduction to the membrane reactor treatment process.
The processing flow of the membrane reactor mainly includes the following key steps:
1. Water inlet and pretreatment: Wastewater first enters the biofilm reactor system. At this stage, large suspended solids and some organic matter are removed through pretreatment facilities (such as screens and grit chambers) to prevent them from clogging subsequent treatment equipment and protecting the biofilm reactor.
2. Biodegradation: The pretreated wastewater enters the bioreactor, where it comes into contact with the biofilm growing on the surface of the filler. The biofilm is a complex ecosystem composed of a variety of microorganisms that adsorb, absorb and degrade organic pollutants in the wastewater, converting them into harmless substances such as water and carbon dioxide. This process is an aerobic biological treatment that requires an adequate supply of oxygen, which is usually achieved through an aeration system.
3. Membrane separation: The water after biodegradation is separated into solid and liquid through the membrane assembly. The membrane assembly usually uses a microfiltration membrane or an ultrafiltration membrane, which has a very small pore size and can effectively intercept biofilm, suspended matter and macromolecular organic matter to ensure the clarity of the effluent. The membrane separation process replaces the secondary sedimentation tank in the traditional process, greatly improving the efficiency of solid-liquid separation and sewage purification.
4. Outlet water and reuse: The water filtered by the membrane module is the treated outlet water, which has excellent water quality, with suspended solids and turbidity close to zero, and bacteria and viruses are largely removed. It can be directly reused as non-drinking municipal water, such as for flushing toilets, green irrigation, road washing, etc.
5. Sludge treatment: The excess sludge accumulated in the biofilm reactor is discharged regularly for further treatment, such as concentration, digestion and dehydration, and finally disposed or recycled. Since the biofilm reactor can operate at high volumetric load and low sludge load, the excess sludge output is relatively low, which reduces the cost of sludge treatment.
6. Membrane cleaning and maintenance: During operation, the membrane assembly will gradually accumulate pollutants, resulting in a decrease in membrane flux. In order to maintain efficient operation of the membrane, the membrane needs to be cleaned regularly. Cleaning methods include physical cleaning (such as backwashing, mechanical scrubbing) and chemical cleaning (such as soaking with chemical agents) to remove the contamination layer on the membrane surface and restore the permeability of the membrane.
membrane reactors have the advantages of high-quality and stable effluent water, small footprint, and convenient operation and management. They are widely used in municipal sewage, industrial wastewater and other fields. By continuously optimizing the treatment process and membrane component performance, membrane reactors will play a more important role in the future water treatment field.
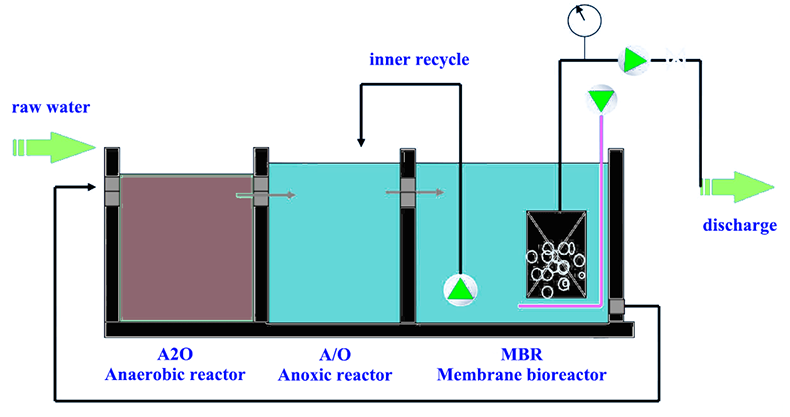